Dynamic modeling and control implementation of a chiller unit
Heremans, Sophie
Promotor(s) :
Lemort, Vincent
Date of defense : 27-Jun-2016/28-Jun-2016 • Permalink : http://hdl.handle.net/2268.2/1391
Details
Title : | Dynamic modeling and control implementation of a chiller unit |
Author : | Heremans, Sophie ![]() |
Date of defense : | 27-Jun-2016/28-Jun-2016 |
Advisor(s) : | Lemort, Vincent ![]() |
Committee's member(s) : | Dechesne, Bertrand ![]() Quoilin, Sylvain ![]() Bertagnolio, Stéphane |
Language : | English |
Number of pages : | 105 |
Keywords : | [fr] Dymola, Chiller, Modeling, Dynamic |
Discipline(s) : | Engineering, computing & technology > Energy |
Funders : | Emerson Climate Technologies |
Target public : | Other |
Institution(s) : | Université de Liège, Liège, Belgique |
Degree: | Master en ingénieur civil électromécanicien, à finalité approfondie |
Faculty: | Master thesis of the Faculté des Sciences appliquées |
Abstract
[en] The aim of this master thesis is to implement a model that will simulate the dynamic behavior of an air-to-water chiller unit in the further with a view of running Hardware-in-the-loop simulations to test hardware control unit. First the calibration and steady state modeling of the chiller components are conducted in EES Software. The calibration is based on steady state experimental data in order to tune components parameters. Then the dynamic model of each component is implemented in Dymola Software. In Dymola, the model of the plate heat evaporator as well as the fin and tubes condenser are based on the finite-control volume method. The scroll compressors are modeled with regression laws based on empirical polynomial equations developed by Emerson. A new mass flow correlation for the EEV is developed especially for the purpose of this study. The equations modeling the fan are obtained by similitudes analysis and involve Rateau's dimensionless coefficients. Finally pressure drops due to piping are determined thanks to experimental data. After validation of each model with experimental data, the components were assembled. To test the modeled unit and observe its behavior during transients a controller is developed. This simple control unit manages the evaporator superheat, the fan, the speed of the variable speed compressor and the fixed speed compressor. A simulation is run to validate the model and to ensure that its behavior matches the one of the real unit under transients. Finally several superheat control strategies are simulated to characterize the benefit on the compressors power consumption.
File(s)
Document(s)
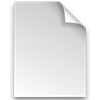

Description:
Size: 12.44 MB
Format: Adobe PDF
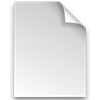

Description: -
Size: 96.77 kB
Format: Adobe PDF
Annexe(s)
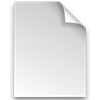

Description:
Size: 62.95 kB
Format: Adobe PDF
Cite this master thesis
APA
Heremans, S. (2016). Dynamic modeling and control implementation of a chiller unit. (Unpublished master's thesis). Université de Liège, Liège, Belgique. Retrieved from https://matheo.uliege.be/handle/2268.2/1391
Chicago
The University of Liège does not guarantee the scientific quality of these students' works or the accuracy of all the information they contain.