Finite element modeling of aeronautic seals
Jetteur, Claire
Promotor(s) :
Bruls, Olivier
Date of defense : 27-Jun-2016/28-Jun-2016 • Permalink : http://hdl.handle.net/2268.2/1536
Details
Title : | Finite element modeling of aeronautic seals |
Translated title : | [fr] Modélisation par éléments finis de joints aéronautiques |
Author : | Jetteur, Claire ![]() |
Date of defense : | 27-Jun-2016/28-Jun-2016 |
Advisor(s) : | Bruls, Olivier ![]() |
Committee's member(s) : | Noels, Ludovic ![]() Ponthot, Jean-Philippe ![]() Gonze, Albert-Paul |
Language : | English |
Number of pages : | 87 |
Discipline(s) : | Engineering, computing & technology > Aerospace & aeronautics engineering |
Institution(s) : | Université de Liège, Liège, Belgique |
Degree: | Master en ingénieur civil en aérospatiale, à finalité approfondie |
Faculty: | Master thesis of the Faculté des Sciences appliquées |
Abstract
[en] Nowadays, numerical simulation is increasingly used, providing tools to reproduce numerically the behavior of a system and solve engineering problems. In sectors such as aeronautics, this tool is essential with the constant process of improvement at the lowest costs, parts becoming more and more complex.
During take-off and landing, an aircraft is subjected to heavy aeronautic loads. To avoid stalling of the aircraft during these two critical phases, moveable devices located on the wings are used to increase the lift of the plane, such as the slat, located on the leading edge of the wing, and the flap, located on the trailing edge. To adapt to the aerodynamic requirements, the latter is divided into two parts: the inboard flap, next to the fuselage, and the outboard flap, next to the wing tip, joined together by an interflap seal. This project focuses on that part.
Used to maintain the sealing against air between the outboard and inboard flap in order to ensure optimal performances, the seal is heavily loaded when activating the flaps. To fulfil such aeronautical constraints (aerodynamic pressure, displacements, altitude, temperature,…), seals made of reinforced elastomer are necessary. The seals studied in this report are made of two main materials: silicone, allowing huge deformation, and glass fiber reinforcements, increasing the rigidity of the seals.
So far, the development of the design, the stiffness and the manufacturing method of the seal was based on development tests as the material properties of this complex material are not known precisely enough to safely predict the behavior of the structure. The objective of this work is to determine the properties of the different materials (silicone and reinforcement) in order to use the results of the finite element analysis with a higher confidence, with a view to cost and time reduction.
To do so, experimental tests (tension, compression and bending) were performed on test specimens, composed of a silicone matrix and different numbers of reinforcement. The material parameters are calculated by matching numerical results obtained by performing finite element analysis with the experimental results.
Through simulations of the test specimens, linear and nonlinear elastic material laws were found to match the experimental results. The obtained behavior laws are then tested in finite products, two different seal models in this case, to check if there are acceptable and validate them.
To conclude, appropriate material laws are found to model the behavior of aeronautical seals. Nevertheless, the laws are different according to the type of solicitation, pure tension/compression or bending, and the number of reinforcements inside the silicone matrix. Moreover, the laws can still be refined and improved to increase the precision of the finite element analysis.
File(s)
Document(s)
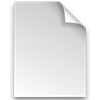

Description:
Size: 4.88 MB
Format: Adobe PDF
Cite this master thesis
The University of Liège does not guarantee the scientific quality of these students' works or the accuracy of all the information they contain.