Travail de fin d'études et stage[BR]- Travail de fin d'études : Preliminary design and analysis of a high temperature heat pump using a centrifugal compressor[BR]- Stage d'insertion professionnelle : Mitis
Hustinx, Nora
Promotor(s) :
Lemort, Vincent
Date of defense : 26-Jun-2023/27-Jun-2023 • Permalink : http://hdl.handle.net/2268.2/17220
Details
Title : | Travail de fin d'études et stage[BR]- Travail de fin d'études : Preliminary design and analysis of a high temperature heat pump using a centrifugal compressor[BR]- Stage d'insertion professionnelle : Mitis |
Author : | Hustinx, Nora ![]() |
Date of defense : | 26-Jun-2023/27-Jun-2023 |
Advisor(s) : | Lemort, Vincent ![]() |
Committee's member(s) : | Hillewaert, Koen ![]() Gendebien, Samuel ![]() Heylen, Martin |
Language : | English |
Keywords : | [en] high temperature heat pump [en] centrifugal compressor [en] python [en] water refrigerant |
Discipline(s) : | Engineering, computing & technology > Energy |
Institution(s) : | Université de Liège, Liège, Belgique |
Degree: | Master en ingénieur civil électromécanicien, à finalité spécialisée en énergétique |
Faculty: | Master thesis of the Faculté des Sciences appliquées |
Abstract
[en] In a context of energy crisis, finding more efficient and viable energy sources is a key research area. The waste heat recovery falls into this topic. Indeed, industrial processes most often waste heat through their operation. A high temperature heat pump is a solution to re-use waste heat in the process.
In this project, a preliminary design of a high temperature heat pump (HTHP) intended for use by small and medium enterprises is developed. Before the definition of the scope, a comprehensive theoretical background on heat pumps and compressors and a state of the art and market overview of the heat pump technology, including the fields of interest and refrigerants, are provided. From there, it is decided to design an HTHP that works with water (R-718) as a refrigerant between an air heat source at 35°C and a water heat sink at 60°C. It will provide 300 kW and heat the sink to 150°C.
An overview of all the configurations studied for HTHPs is provided. Five of them appear particularly suitable for this application: the single-stage basic cycle, the single-stage cycle with an added internal heat exchanger (IHX), the single-stage turbine-compressor cycle with IHX, the two-stage refrigerant injection cycle with a flash tank (FT) and the two-stage refrigerant injection cycle with an FT and an IHX. In order to simulate those configurations and to determine which is the most suited in this context, the relevant components are modeled in the most general way. This includes the condenser, evaporator, IHX, FT, expansion valve, t-pipe with two inlets, compressor and turbine. According to those models, six configurations are tested, the five mentioned and a four-stage refrigerant injection cycle with three FTs.
The results are then discussed. In particular, the coefficient of performance (COP) of the machine is compared to the COP of the respective Carnot cycle. Moreover, the maximum temperature occurring in the cycle, the compression and expansion ratios, the required mass flow rates of the refrigerant and air, the total power consumed, and the heat exchangers effectiveness and UA coefficients are discussed. It is concluded that the four-stage configuration is the most suitable for this specific HTHP.
Finally, from the results of the simulations, a preliminary design of the four compressors is carried out. It starts with a theoretical study of each impeller inlet geometry, and is completed by a comparison with the results obtained with a software that also provides the geometry of each compressor.
File(s)
Document(s)
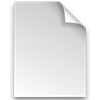

Description:
Size: 8.35 MB
Format: Adobe PDF
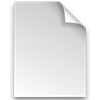

Description: -
Size: 136.65 kB
Format: Adobe PDF
Annexe(s)
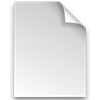

Description:
Size: 81.43 kB
Format: Adobe PDF
Cite this master thesis
The University of Liège does not guarantee the scientific quality of these students' works or the accuracy of all the information they contain.