Selective recovery of graphite from the hydrometallurgical processing of Lithium Ion Batteries
Jha, Smriti Anand
Promoteur(s) :
Gaydardzhiev, Stoyan
Date de soutenance : 4-sep-2023/5-sep-2023 • URL permanente : http://hdl.handle.net/2268.2/18376
Détails
Titre : | Selective recovery of graphite from the hydrometallurgical processing of Lithium Ion Batteries |
Titre traduit : | [fr] Selective recovery of graphite from the hydrometallurgical processing of Lithium Ion Batteries |
Auteur : | Jha, Smriti Anand ![]() |
Date de soutenance : | 4-sep-2023/5-sep-2023 |
Promoteur(s) : | Gaydardzhiev, Stoyan ![]() |
Membre(s) du jury : | Mahmoud, Abdelfattah ![]() Lambert, Fanny ![]() Job, Nathalie ![]() Hernadi, Klara |
Langue : | Anglais |
Nombre de pages : | 109 |
Mots-clés : | [fr] Flotation [fr] Graphite recycling [fr] Leaching [fr] Electrochemical Characterization |
Discipline(s) : | Ingénierie, informatique & technologie > Ingénierie chimique |
Centre(s) de recherche : | Gemme and Greenmat :University of Liege |
Intitulé du projet de recherche : | Selective recovery of Graphite from Hydrometallurgical Processing of Lithium Ion batteries |
Public cible : | Chercheurs Professionnels du domaine Etudiants Grand public Autre |
Institution(s) : | Université de Liège, Liège, Belgique |
Diplôme : | Master : ingénieur civil en chimie et science des matériaux, à finalité spécialisée en Advanced Materials - Innovative Recycling |
Faculté : | Mémoires de la Faculté des Sciences appliquées |
Résumé
[fr] Graphite stands as the cutting-edge choice for anode material in lithium-ion batteries (LIBs), a technology prevalent in countries such as China. This makes it a critical raw material for Europe. While LIB recycling at an industrial scale typically recovers cathode active materials (Co, Mn, Ni) through hydro or pyrometallurgical methods, the valuable graphite component often gets lost in the process as a leaching residue ending up in landfill or used as reducing agent in pyro plants. This study focuses on the recovery and purification of the graphite via froth flotation and leaching after leaching of black mass for Co, Ni, Mn recovery.
Flotation was the first approach that was used to further purify the leaching residue. The study concluded that TT-LR (Thermally treated (BM) leaching residue) showed the best separation efficiency and helped to achieve overflow fraction with a carbon grade of 94% and recovery of 55% under the following parameters: 60 g/t Frother, pulp density-10%, airflow-2 L/min and rotational speed-700 rpm. Both Direct re-leaching on residue and re-leaching after flotation was investigated to optimise the graphite recovery and purification process. The results indicated that the re-leaching step carried on the flotation overflow with the initial grade of 94% was carried out at a pH of 1.5 and a 10% pulp density, successfully eliminating elemental copper, aluminium, and cathode active materials. As a result, the carbon purity is boosted to 98%.
The electrochemical properties of the recycled graphite with a purity of 98% were investigated and compared to directly scrapped graphite from copper of manually dismantled spent LIBs. An additional heat treatment was applied to the material to evaluate its impact. Heat-treated reclaimed graphite achieves a specific capacity of 352 mAhg-1 over 50 cycles. This material exhibits improved capacity retention during electrochemical cycling at various rates (C/20, C/10, and C/5) as shown in rate capability tests. The cyclic voltammetry test confirms the improvement of electrochemical properties after heat treatment and therefore confirms the usability of recycled graphite in combination with primary graphite in commercial battery manufacturing.
Fichier(s)
Document(s)
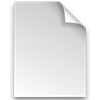

Description: Selective Recovery of Graphite from Hydrometallurgical Processing of Lithium Ion Batteries
Taille: 4.34 MB
Format: Adobe PDF
Citer ce mémoire
APA
Jha, S. A. (2023). Selective recovery of graphite from the hydrometallurgical processing of Lithium Ion Batteries. (Unpublished master's thesis). Université de Liège, Liège, Belgique. Retrieved from https://matheo.uliege.be/handle/2268.2/18376
Chicago
L'Université de Liège ne garantit pas la qualité scientifique de ces travaux d'étudiants ni l'exactitude de l'ensemble des informations qu'ils contiennent.