Travail de fin d'études et stage[BR]- Travail de fin d'études : Characterization of Friction Coefficient at the Tip-Base Interface of Scroll Compressors[BR]- Stage
Martin, Antoine
Promotor(s) :
Bruls, Olivier
;
Salles, Loïc
Date of defense : 24-Jun-2024/25-Jun-2024 • Permalink : http://hdl.handle.net/2268.2/20451
Details
Title : | Travail de fin d'études et stage[BR]- Travail de fin d'études : Characterization of Friction Coefficient at the Tip-Base Interface of Scroll Compressors[BR]- Stage |
Author : | Martin, Antoine ![]() |
Date of defense : | 24-Jun-2024/25-Jun-2024 |
Advisor(s) : | Bruls, Olivier ![]() Salles, Loïc ![]() |
Committee's member(s) : | Gilet, Tristan ![]() Quoirin, Vincent Lenaerts, Simon |
Language : | English |
Number of pages : | 70 |
Keywords : | [en] Compressor [en] Friction [en] Tribology [en] Lubrication [en] Scroll Compressors |
Discipline(s) : | Engineering, computing & technology > Mechanical engineering |
Funders : | Copeland |
Institution(s) : | Université de Liège, Liège, Belgique |
Degree: | Master : ingénieur civil mécanicien, à finalité spécialisée en mécatronique |
Faculty: | Master thesis of the Faculté des Sciences appliquées |
Abstract
[en] Friction is the main mechanical loss taking place inside scroll compressors. It can lead to wear and
reduces the reliability and service life of the compressors. The friction phenomenon needs to be understood and modelled so that the friction can ultimately be reduced and correctly taken into account during the design of the scroll compressors. This thesis researches and develops a friction model for the tip-base interface contact of the scroll, in order to obtain a friction coefficient depending on the operating conditions of the compressor.
This model is implemented in Python. It corresponds to a mixed lubrication model able to model
friction for all operating conditions and lubrication regimes. The model is discrete, and the tip-base
interface is thus discretized using a regular mesh composed of quadrangle elements. The model is fed with different inputs. MBD simulations are used to generate the tip-base gap geometry. The boundary and axial load are derived from analytical computations, while the fluid and material parameters are sourced from the literature. It is composed of a fluid and a dry model that are combined to give the most general model possible. The fluid model is based on the Reynolds equation that is averaged in order to take into account the influence of the rough surface on the lubricant flow when the lubricant film is very small. The Reynolds equation is solved by an iterative process using finite difference method. The dry model is based on the stochastic model of Greenwood-Tripp that makes assumptions on the statistical distribution of the surface roughness. The two models are then assembled, and the tip-base gap is adjusted through the offset film thickness determined using a root-finding algorithm on the load balance condition.
The fluid model is verified using known academic results, and the numerical solution is optimized
through a convergence study. The complete implemented model is then used to understand the frictional behaviour of the tip-base contact, first, for operating conditions -5 to 60°C at 8000 RPM. The average friction coefficient has been found to be 0.023 with a fluid friction significantly lower than
the dry one. The influence of the rotational speed is then explored by studying the results at 2900
and 6000 RPM. It is shown that the friction coefficient decreases when the speed increases, as the
speed increase tends to separate the surfaces. The influence of operating conditions is finally studied by changing the inlet and outlet temperature to 8 to 45°C and keeping the speed at 2900 RPM. It is shown that the friction coefficient decreases when the temperature ratio decreases as the inlet boundary pressure is higher for these conditions. Overall, it is shown that the average friction coefficient for a complete revolution of the scroll varies between 0.02 and 0.03, suggesting that the 0.04 value used in Copeland computations is slightly overestimated. Stribeck curve for this contact is finally derived.
This curve shows that at low speeds, the coefficient decreases when speed increases, as the surfaces are separated. At high speeds, the coefficient increases with the rotational speed, as the viscous shear stresses are increased.
File(s)
Document(s)
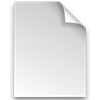

Description:
Size: 49.62 MB
Format: Adobe PDF
Annexe(s)
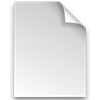

Description:
Size: 59.89 kB
Format: Adobe PDF
Cite this master thesis
APA
Martin, A. (2024). Travail de fin d'études et stage[BR]- Travail de fin d'études : Characterization of Friction Coefficient at the Tip-Base Interface of Scroll Compressors[BR]- Stage. (Unpublished master's thesis). Université de Liège, Liège, Belgique. Retrieved from https://matheo.uliege.be/handle/2268.2/20451
Chicago
The University of Liège does not guarantee the scientific quality of these students' works or the accuracy of all the information they contain.