Travail de fin d'études et stage[BR]- Travail de fin d'études : Modelling of composite pressure vessels (carbon-epoxy COPV) for the FEM approach[BR]- Stage
Tshilolo Muepu Malaïka, Josémaria
Promotor(s) :
Bruyneel, Michaël
Date of defense : 24-Jun-2024/25-Jun-2024 • Permalink : http://hdl.handle.net/2268.2/20462
Details
Title : | Travail de fin d'études et stage[BR]- Travail de fin d'études : Modelling of composite pressure vessels (carbon-epoxy COPV) for the FEM approach[BR]- Stage |
Author : | Tshilolo Muepu Malaïka, Josémaria ![]() |
Date of defense : | 24-Jun-2024/25-Jun-2024 |
Advisor(s) : | Bruyneel, Michaël ![]() |
Committee's member(s) : | Ponthot, Jean-Philippe ![]() Strepenne, François |
Language : | English |
Number of pages : | 64 |
Keywords : | [en] Composite pressure vessel [en] Non-geodesic [en] Filament winding [en] Winding angle [en] Slippage coefficient |
Discipline(s) : | Engineering, computing & technology > Mechanical engineering |
Target public : | Researchers Professionals of domain Student |
Institution(s) : | Université de Liège, Liège, Belgique |
Degree: | Master : ingénieur civil mécanicien, à finalité spécialisée en mécatronique |
Faculty: | Master thesis of the Faculté des Sciences appliquées |
Abstract
[en] Facing the energy crisis and the necessity to reduce CO2 and greenhouse gas emissions,
hydrogen has emerged as a key option in the decarbonization of fields such as aerospace and
automotive. Indeed, hydrogen constitutes a solution in the storage and transportation of
energy. Typically, hydrogen is stored in Composite Overwrapped Pressure Vessels (COPVs)
which have a better strength-to-weight ratio than traditional metallic pressure vessels. However, COPVs are still subject to improvement in the filament winding process which is greatly
responsible for the damage resistance and the fatigue behavior.
This Master thesis addresses the implementation of a model predicting the evolution of the
winding angle on the dome of cylindrical pressure vessels. The winding angle is an important
parameter in the determination of the mechanical behavior of composite pressure vessels. In
order to enlarge the possibility of winding trajectories, non-geodesic winding is implemented in
MATLAB. The solution of the non-geodesic equation is computed using the 4th-order Runge
Kutta method with a constant discretization over the dome profile. Then, the approach is
extended to a multi-layer structure predicting the winding angle on an arbitrary pseudo-ply
different from an ellipse.
Finally, a methodology to mesh a lay-up is implemented by defining the nodes, the elements,
and the winding angle associated with each element. The finite element model is then exported
in SAMCEF BACON for later simulations. This results in a more realistic dome modelling by
considering the different plies and the non-geodesic trajectories in the filament winding process.
File(s)
Document(s)
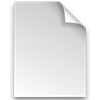

Description:
Size: 7.56 MB
Format: Adobe PDF
Cite this master thesis
APA
Tshilolo Muepu Malaïka, J. (2024). Travail de fin d'études et stage[BR]- Travail de fin d'études : Modelling of composite pressure vessels (carbon-epoxy COPV) for the FEM approach[BR]- Stage. (Unpublished master's thesis). Université de Liège, Liège, Belgique. Retrieved from https://matheo.uliege.be/handle/2268.2/20462
Chicago
The University of Liège does not guarantee the scientific quality of these students' works or the accuracy of all the information they contain.