Validation of a CFD tool on an axial compressor using a polyhedral mesh
Bobach, Billy-Joe
Promoteur(s) :
Terrapon, Vincent
Date de soutenance : 6-sep-2018/7-sep-2018 • URL permanente : http://hdl.handle.net/2268.2/5218
Détails
Titre : | Validation of a CFD tool on an axial compressor using a polyhedral mesh |
Auteur : | Bobach, Billy-Joe ![]() |
Date de soutenance : | 6-sep-2018/7-sep-2018 |
Promoteur(s) : | Terrapon, Vincent ![]() |
Membre(s) du jury : | Noels, Ludovic ![]() Ranjan, Saha |
Langue : | Anglais |
Mots-clés : | [en] CFD [en] Compressor [en] Aerodynamics [en] Star-CCM+ [en] Polyhedral mesh [en] Validation [en] Gas turbine |
Discipline(s) : | Ingénierie, informatique & technologie > Ingénierie mécanique |
Public cible : | Professionnels du domaine Etudiants |
Institution(s) : | Université de Liège, Liège, Belgique Siemens Turbomachinery AB, Finspång, Suede |
Diplôme : | Master en ingénieur civil en aérospatiale, à finalité spécialisée en "turbomachinery aeromechanics (THRUST)" |
Faculté : | Mémoires de la Faculté des Sciences appliquées |
Résumé
[en] An alternative CFD code is tested and validated to complement the design work flow of a compressor for a mid-sized gas turbine for power generation. Usually, when an expensive 3D simulation of the whole compressor is needed, a structured mesh is used, due to its accuracy and minimal cost. Unstructured meshes on the other hand are uncommon in this context. However, when the literature mentions unstructured meshes, it refers to tetrahedral meshes. Literature indicates that polyhedral unstructured meshes, as in Star-CCM+, are far superior than the conventional tetrahedral unstructured meshes in both accuracy and cost. In some circumstances the polyhedral unstructured mesh may be able to compete with a structured hexahedral mesh, especially, when the flow deviates from the design flow path (e.g. separation, stall). A comparison of the accuracy or cost is, however, not the topic of the report. Instead the project sets the foundation for further work that may go in this direction. A comparison with experimental data and results from a low-fidelity solver (Multip) at different operating conditions is undertaken. The geometrical flexibility of the unstructured meshing is exploited to incorporate more complicated geometrical features (i.e. leakage stubs, tip clearance), that require extensive effort when meshing a structured mesh or that require work-arounds and modelling.
After an extensive mesh study and other sensitivity studies, a speed line and an operating line (of the whole gas turbine) are simulated with two common turbulence models. It is found that there is a large mismatch of the absolute values of engineering parameters, such as pressure ratio, mass flow and polytropic efficiency. In fact, there appears to be an offset by -1.5% in efficiency and -2.0kg/s after matching the pressure ratio, when comparing with the experiments. Although this is in fact a significant underprediction, the general trends do match. Especially the SST turbulence model captures the shape of the performance curves very well. It also accurately captures the choking at high corrected engine speed, where the other 3D CFD solver fails. Late in the project it was discovered that the offset may be caused by wrongly chosen gas properties (specific heat). A more realistic choice seems to increase both mass flow and efficiency at constant pressure ratio.
Unfortunately, due to limited time and resources, a number of open questions remain. Especially the gas properties deserve more work in the future, but also the turbulence modelling, the mesh study and the details of the flow field need to be reviewed. The main objective of building the geometry and the mesh, converging a solution and obtaining a match with experimental data was achieved. The time was spent evenly on most aspects that are cause for concern and the confidence in the results can therefore be reasonable. For the Star-CCM+ code to be included in the design process in some way, the remaining sources of uncertainty need to be investigated further. Despite the remaining open questions, a working model could be established, setting a solid foundation for future work.
Secondary flow produces a large amount of aerodynamic loss especially in the rear stages and has a big influence on the surge margin. The various 3D features (lean, sweep, bow) seem to have potential to decrease the secondary flow and increase aerodynamic performance according to literature. However, these features were not investigated thoroughly in SIT compressors. In this project a new CFD tool (STAR-CCM+) will be used to validate the aerodynamic performance of a reference compressor. The student should work with the tool from scratch to the final model (i.e. from geometry, meshing to final 3D steady simulation), and finally compare and analyse the outcome with available engine data. Thereafter blading in the rear stages is required to be modified using advance 3D blading features and foresee any obvious benefit.
Fichier(s)
Document(s)
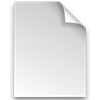

Description:
Taille: 7.14 MB
Format: Adobe PDF
Citer ce mémoire
L'Université de Liège ne garantit pas la qualité scientifique de ces travaux d'étudiants ni l'exactitude de l'ensemble des informations qu'ils contiennent.