Validation of an online 3D scanner for bulk solids size analysis operating in harsh environment
Parmar, Arpit Singh
Promotor(s) :
Pirard, Eric
Date of defense : 24-Aug-2018 • Permalink : http://hdl.handle.net/2268.2/7259
Details
Title : | Validation of an online 3D scanner for bulk solids size analysis operating in harsh environment |
Author : | Parmar, Arpit Singh ![]() |
Date of defense : | 24-Aug-2018 |
Advisor(s) : | Pirard, Eric ![]() |
Committee's member(s) : | Rosenkranz, Jan
Gaydardzhiev, Stoyan ![]() Nguyen, Frédéric ![]() Materne, Jean |
Language : | English |
Number of pages : | 164 |
Keywords : | [en] Particle size distribution [en] Comminution [en] Image analysis [en] Image segmentation [en] Laser triangulation [en] Automation [en] Sampling [en] Sieving [en] Limestone [en] Lime [en] Calcination [en] Closed side setting [en] Run of mine |
Discipline(s) : | Engineering, computing & technology > Geological, petroleum & mining engineering |
Research unit : | Géoressources minérales & Imagerie géologique |
Name of the research project : | Validation of an online 3D scanner for bulk solids size analysis operating in harsh environment |
Target public : | Researchers Professionals of domain Student |
Institution(s) : | Université de Liège, Liège, Belgique |
Degree: | Master en ingénieur civil des mines et géologue, à finalité spécialisée en "geometallurgy (EMERALD)" |
Faculty: | Master thesis of the Faculté des Sciences appliquées |
Abstract
[en] Sampling and screening has been a popular method to evaluate size distribution of the fragmented material. However, this method is often considered as impractical especially when quick feedback is required for process control. Image analysis based online measurement systems (also known as machine vision systems) offer a quick, inexpensive and non-invasive way of determining the size distribution of fragmented rock (Thurley, 2002).
In this thesis, a new online 3D size measurement system (Laser Sieve) has been applied in an industrial project of Lhoist for optimization of limestone production process with regards to the minimization of fines generation. This production process involved three stages: Blasting, Primary crushing, and Secondary crushing wherein, Laser Sieve was installed to monitor the Primary Jaw Crusher product size distribution. A process audit has been conducted using Laser Sieve and Belt Scales by studying each of these production stages to identify the factors responsible for fines generation and limit their effects. Firstly, the production process was studied theoretically using some theoretical product distribution curves given by equipment manufacturers. Based on this, theoretical solutions were derived to minimize the generation of fines for the limestone production process of Jemelle. Secondly, some preliminary studies were done to determine the existing working performance and also to establish correlations between Belt Scale readings of feed and product fractions. These studies showed that for limiting the generation of fines, it is necessary to reduce fines generation in the run of mine (ROM). A theoretical simulation was also executed using Microsoft Excel for the production process at Jemelle, which showed inconsistencies when compared to the actual production figures.
After these preliminary studies, plant scale investigations were conducted to determine the preferred blasting conditions and to optimize the closed side setting (CSS) of the Primary Jaw Crusher. No specific regulation of Secondary Roll Crusher could be tried owing to its open circuit operation at Jemelle. A part of the blasted material (i.e., the 0-120 mm size fraction in ROM) was characterized using sampling and screening method. Boulder tests were conducted by feeding the Jaw Crusher with three types of boulders (of different sizes) from the quarry. Subsequently, the CSS of the Jaw Crusher was modified. Laser Sieve and Belt Scales facilitated these investigations by analyzing the Jaw Crusher product size distribution and recording the tonnages of feed and product fractions respectively. The results showed that it is preferred to feed the Jaw Crusher with a lower top size in ROM. While a larger CSS of primary crusher resulted in less production of fines, which was not in accord with the theoretical solutions.
A mass balance was performed to back-calculate the secondary crusher product distributions, which showed a deviation from the reference theoretical product distribution curve. Therefore, it was suggested that this unexpected phenomenon could be the result of either the overloading of secondary double deck screens or it could be the actual distribution given by the secondary crusher. Some more investigations have been suggested to ascertain the causes and proceed further with the optimization of the plant. Finally, a demonstration of automation in the existing limestone preparation plant is presented with the help of predictive modelling and integration of Laser Sieve in the production process.
File(s)
Document(s)
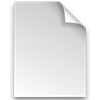

Description: -
Size: 59.75 MB
Format: Adobe PDF
Cite this master thesis
APA
Parmar, A. S. (2018). Validation of an online 3D scanner for bulk solids size analysis operating in harsh environment. (Unpublished master's thesis). Université de Liège, Liège, Belgique. Retrieved from https://matheo.uliege.be/handle/2268.2/7259
Chicago
The University of Liège does not guarantee the scientific quality of these students' works or the accuracy of all the information they contain.