Quality assessment of highly productive selective laser melting processes
Ducarme, Paul
Promotor(s) :
Béchet, Eric
Date of defense : 9-Sep-2019/10-Sep-2019 • Permalink : http://hdl.handle.net/2268.2/7846
Details
Title : | Quality assessment of highly productive selective laser melting processes |
Translated title : | [fr] Évaluation de la qualité des processus de fusion laser sélective hautement productifs |
Author : | Ducarme, Paul ![]() |
Date of defense : | 9-Sep-2019/10-Sep-2019 |
Advisor(s) : | Béchet, Eric ![]() |
Committee's member(s) : | Ponthot, Jean-Philippe ![]() Mertens, Anne ![]() Cocle, Roger |
Language : | English |
Number of pages : | 120 |
Keywords : | [en] Selective laser melting [en] AlSi10Mg [en] 316L [en] Highly productive [en] Experiments [en] Density [en] Surface roughness [en] Layer thickness [en] Parameters [en] Power [en] Scanning speed [en] Hatch spacing |
Discipline(s) : | Engineering, computing & technology > Mechanical engineering Engineering, computing & technology > Materials science & engineering |
Funders : | Any-Shape |
Target public : | Researchers Professionals of domain Student General public |
Institution(s) : | Université de Liège, Liège, Belgique |
Degree: | Master en ingénieur civil mécanicien, à finalité spécialisée en génie mécanique |
Faculty: | Master thesis of the Faculté des Sciences appliquées |
Abstract
[en] The thesis aims at determining suitable selective laser melting process parameters enabling high productivity and sufficient part quality, for two materials: the aluminium alloy AlSi10Mg and the stainless steel SS316L.
To do that, the concept of productivity is first defined. On that basis, a strategy to optimize it is determined. It consists of finding adequate exposure parameters (power, scanning speed, hatch spacing, contour powers and contour scanning speeds) leading to a high relative density and low surface roughness, when the layer thickness is set to 0.1 mm (AlSi10Mg) and 0.08 mm (SS316L).
Experiments consisting of printing small cubes with different sets of parameters are conducted. Selecting test series parameters is reasoned using an index, which provides an estimation of the lack of fusion porosity that should be expected given a combination of power, scanning speed, hatch spacing and layer thickness.
Relative density is measured through Archimede’s method and micrography. AlSi10Mg and SS316L samples associated to a high index show lack-of-fusion pores. Besides, AlSi10Mg samples manufactured with low scanning speeds are subjected to spherical porosity, due to hydrogen bubbles that had time to grow in the melt pool before being trapped by solidification, most likely. SS316L samples present keyhole pores at high-energy-density regimes and porosity due to Plateau-Rayleigh instability at high-power-and-scanning-speed regimes.
Regarding surface quality, AlSi10Mg samples show a lower roughness when linear energy density is increased using two pre-contours, whereas SS316L samples present a better surface quality with one post-contour. Best surface roughness obtained after sandblasting is 6 μm for AlSi10Mg and 7 μm for SS316L.
Based on the conclusions of the experiments, a model is built to delimit windows of parameters leading to a sufficiently high density. Optimal sets regarding productivity are selected inside the windows. Predicted build rates are 16.5 mm3/s and 9.6 mm3/s for AlSi10Mg and SS316L, respectively. They increase current volume build rates by 58% and 159%, respectively.
File(s)
Document(s)
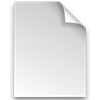

Description: null
Size: 256.61 MB
Format: Adobe PDF
Cite this master thesis
APA
Ducarme, P. (2019). Quality assessment of highly productive selective laser melting processes. (Unpublished master's thesis). Université de Liège, Liège, Belgique. Retrieved from https://matheo.uliege.be/handle/2268.2/7846
Chicago
The University of Liège does not guarantee the scientific quality of these students' works or the accuracy of all the information they contain.