Final work : Conjugate heat transfer analysis and comparison of the results with different CFD modeling methods in FINE/Open
Jawad, Amir-Alexandru
Promotor(s) :
Terrapon, Vincent
Date of defense : 9-Sep-2019/10-Sep-2019 • Permalink : http://hdl.handle.net/2268.2/8127
Details
Title : | Final work : Conjugate heat transfer analysis and comparison of the results with different CFD modeling methods in FINE/Open |
Author : | Jawad, Amir-Alexandru ![]() |
Date of defense : | 9-Sep-2019/10-Sep-2019 |
Advisor(s) : | Terrapon, Vincent ![]() |
Committee's member(s) : | Lohitasyudu, Gorli
Dimitriadis, Grigorios ![]() |
Language : | English |
Keywords : | [en] Conjugated Heat Transfer [en] Radiator [en] Computational Fluid Dynamics [en] Heat Exchanger |
Discipline(s) : | Engineering, computing & technology > Aerospace & aeronautics engineering |
Target public : | General public |
Institution(s) : | Université de Liège, Liège, Belgique |
Degree: | Master en ingénieur civil en aérospatiale, à finalité spécialisée en "turbomachinery aeromechanics (THRUST)" |
Faculty: | Master thesis of the Faculté des Sciences appliquées |
Abstract
[en] This thesis presents a detailed analysis of different CFD modeling methods of heat exchangers, with the Numeca FineTM/Open solver. In this case, the heat exchanger is represented by an automotive engine radiator. Apart from this study, this thesis also presents a detailed analysis of the coolant flow in the pipes of the engine radiator.
The first investigation done in this thesis regarded the study of the coolant flow alone, by using the density-based solver with FineTM/Open. In this case, only the radiator coolant walls were selected from the CAD model. This investigation was met with very slow mass flow convergence, since the geometry and velocity of the coolant created a far from ideal scenario for any density-based solver. Ideally, the pressure-based solver would have been much better suited for this application. Also, this a study of different turbulence models was therefore performed, for meshes with and without wall functions, and revealed that the density-based solver predicts more consistent results when turbulence models with extended wall functions are used.
The second part of the thesis involved the study of different modeling methods for the heat exchanger. The modeling methods in question are the full 3D conjugate heat transfer model, the macro model and the thin-shell model.
The CFD analysis of the 3D conjugate heat transfer model was first performed. The mesh generated for this model had over 194 million cells. The computations were carried out at multiple air speeds, in order to establish benchmark results for the other two models. Furthermore, the heat load curve and pressure drop curve obtained from this model were used for the implementation of the porous media model and heat load curve macro model. To gather all this data, enormous computational resources were required, thus making it infeasible.
In the case of the macro model, the 3D engine radiator model part is replaced by a rectangular box with cartesian mesh, where the porous media is used to account for the pressure loss, and the heat load curve based macro model is used to account for the heat rejection of the coolant. The inlet coolant temperature can be computed by imposing the required heat rejection rate, or the heat rejection rate can be computed by imposing the inlet coolant temperature
OpenLabsTM is used for the implementation of the macro model in the FineTM/Open Solver. Several modifications of the script were performed in order to allow the study of configurations with multiple fluid passes. Validations tests showed that the new macro model works properly. These validation tests showed that, when compared to the 3D model, the macro model predicted accurate results, within 5% of difference. Also, the macro model presented a very important advantage in terms of computational cost. The mesh size, CPU/iteration and normalized CPU time decreased by more than 90%, while using four times fewer processors.
For the thin-shell model, the thickness of the fins and pipes is not modeled physically. Here, the 2D conduction equation of the solid pipes and fins is solved, by imposing the values of thickness and thermal conductivity. The advantage of this model, when compared with the 3D model, is that the mesh size has been reduced by 83%, while the CPU/iteration has been reduced by 58%, using three times fewer processors.
File(s)
Document(s)
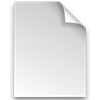

Description:
Size: 5.07 MB
Format: Adobe PDF
Cite this master thesis
The University of Liège does not guarantee the scientific quality of these students' works or the accuracy of all the information they contain.