Modelling of the braiding process based on analytical and kinematic approaches[BR]- Integration internship
Altemirov, Aimourza
Promotor(s) :
Bruyneel, Michaël
;
De Vincenzo, Pascal
Date of defense : 24-Jun-2021/25-Jun-2021 • Permalink : http://hdl.handle.net/2268.2/11479
Details
Title : | Modelling of the braiding process based on analytical and kinematic approaches[BR]- Integration internship |
Author : | Altemirov, Aimourza ![]() |
Date of defense : | 24-Jun-2021/25-Jun-2021 |
Advisor(s) : | Bruyneel, Michaël ![]() De Vincenzo, Pascal |
Committee's member(s) : | Dimitriadis, Grigorios ![]() Noels, Ludovic ![]() Bruls, Olivier ![]() |
Language : | English |
Keywords : | [en] Braiding [en] Composites |
Discipline(s) : | Engineering, computing & technology > Aerospace & aeronautics engineering |
Research unit : | Open Engineering |
Name of the research project : | ViBra |
Target public : | Researchers Professionals of domain Student General public |
Institution(s) : | Université de Liège, Liège, Belgique |
Degree: | Master en ingénieur civil en aérospatiale, à finalité spécialisée en "aerospace engineering" |
Faculty: | Master thesis of the Faculté des Sciences appliquées |
Abstract
[en] Composite materials are increasingly used in the aerospace, automotive, biomedical and many more industries as substitutes to their conventional metallic counterparts. One particular kind of composite materials are the braided composites that have become the subject of great interest in recent years. Interest in these materials is justified not only by their excellent mechanical properties and behaviour, but also by the cost and time effectiveness of the braiding process.
One aspect of the braiding process that is still generally lacking and needs improvement is the control of the machine, i.e. the correlation between the machine parameters and the geometry of the resulting braid. Experienced machine operators are able to manufacture desired, or acceptable, preforms but excessive trial and errors are usually needed, especially when complex shapes are required. As a result, the manufacturing process can be inefficient. To overcome this limitation, numerical models predicting the braid parameters, on which the mechanical properties of the material are directly dependent, are developed. In this work, two such models are implemented and used to analyse the braid structure for different mandrel shapes in the case of 2D biaxial braiding. Both are kinematic models which, although not as accurate, benefit from short calculation times compared to the more detailed finite element approach. Also, the models contain hypotheses such as the neglect of yarn interaction and yarn slip on the mandrel as well as the assumption of straight yarns in the convergence zone, which could lead to systematic errors.
File(s)
Document(s)
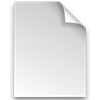

Description: -
Size: 23.24 MB
Format: Adobe PDF
Annexe(s)
Cite this master thesis
APA
Altemirov, A. (2021). Modelling of the braiding process based on analytical and kinematic approaches[BR]- Integration internship. (Unpublished master's thesis). Université de Liège, Liège, Belgique. Retrieved from https://matheo.uliege.be/handle/2268.2/11479
Chicago
The University of Liège does not guarantee the scientific quality of these students' works or the accuracy of all the information they contain.