Master thesis : Design of a Blade - Hub Joint for a Built-Up Propeller
Zar Ni
Promoteur(s) : Kaeding, Patrick ; Kluss, Jörn
Date de soutenance : 19-sep-2022 • URL permanente : http://hdl.handle.net/2268.2/16493
Détails
Titre : | Master thesis : Design of a Blade - Hub Joint for a Built-Up Propeller |
Auteur : | Zar Ni ![]() |
Date de soutenance : | 19-sep-2022 |
Promoteur(s) : | Kaeding, Patrick
Kluss, Jörn |
Membre(s) du jury : | Ducoin, Antoine
Bekhit, Adham |
Langue : | Anglais |
Nombre de pages : | 135 |
Mots-clés : | [fr] built-up propeller [fr] ice class [fr] ice strengthening [fr] blade-hub joint [fr] bolted joint [fr] shrink fit or keyless fitting |
Discipline(s) : | Ingénierie, informatique & technologie > Ingénierie mécanique |
Institution(s) : | Université de Liège, Liège, Belgique |
Diplôme : | Master : ingénieur civil mécanicien, à finalité spécialisée en "Advanced Ship Design" |
Faculté : | Mémoires de la Faculté des Sciences appliquées |
Résumé
[fr] ABSTRACT
With the enormous demands and busy schedules of water transportation by the sea-going
vessels, the propulsion system and components are taking part in one of significant roles. In
order to navigate the ship into the water, the marine propellers are crucial to be efficiently and
safely designed. Typically there are two types of propellers: fixed pitch propeller (FPP) and
controllable pitch propeller (CPP), depending on application and mission. Unlike CPP, a
built-up propeller does not include a hydraulic system to control the pitch of the blades but
each blade can be replaced in the case of damage.
This thesis is specifically focused on the design of the blade and hub joint for a built-up
propeller. Additionally, it is intended for the application of ice class for the ship operating in
the Baltic Sea with the ice strengthening materials. There are some obvious benefits of using
built-up propellers. It is a comparatively much simpler and faster change of blades than
conventional mono-block propellers without the need for dry docking and dismounting
facilities if the blades are necessary to be repaired and replaced.
For the blade-hub joint design, there are some possible configurations having their own
benefits and drawbacks. But finally bolted joint design was selected in the aspects of flexible
manufacturing capabilities, easy to mount or dismount the blade on the hub with less effort,
with the least impact on vessel operation. Blades are mounted on the hub and the hub
assembly is connected to the propeller shaft. There are some available shaft connection
methods. Considering the design aspects to support the structure of the hollow hub, and with
experiences and suggestions from (MMG personal communication), shrink fit or keyless
fitting was chosen.
A detailed 3D of the built-up propeller assembly was modelled in Rhino. Also, Siemens NX
was used for blade fillet and detailed bolt threads modelling. Blade-hub assembly design was
developed complying with GL and Finnish-Swedish Ice Class Rules. The special bolts to
connect the blade and hub were designed according to VDI2230, DIN EN ISO 3506-1 and
ANSI/ASME B1 standards. Analytical strength calculations for the bolted joint have been
performed and the results were compared to Ansys structural analysis for different load cases
and FE models to get a safe and efficient design.
Fichier(s)
Document(s)
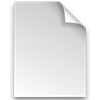

Description:
Taille: 11.05 MB
Format: Adobe PDF
Citer ce mémoire
L'Université de Liège ne garantit pas la qualité scientifique de ces travaux d'étudiants ni l'exactitude de l'ensemble des informations qu'ils contiennent.