Simulation workflow of filament wound carbon composite tanks for pressurized hydrogen storage
Ali, Nazim
Promotor(s) :
Rigo, Philippe
Academic year : 2022-2023 • Permalink : http://hdl.handle.net/2268.2/18048
Details
Title : | Simulation workflow of filament wound carbon composite tanks for pressurized hydrogen storage |
Author : | Ali, Nazim ![]() |
Advisor(s) : | Rigo, Philippe ![]() |
Committee's member(s) : | Rigo, Philippe ![]() |
Language : | English |
Number of pages : | 115 |
Keywords : | [fr] Composite Overwrapped Pressure Vessel (COPV) |
Discipline(s) : | Engineering, computing & technology > Civil engineering |
Institution(s) : | Université de Liège, Liège, Belgique |
Degree: | Master : ingénieur civil mécanicien, à finalité spécialisée en "Advanced Ship Design" |
Faculty: | Master thesis of the Faculté des Sciences appliquées |
Abstract
[fr] Manufacturing of filament wound composite overwrapped pressure vessels (COPVs) is a complicated process in which the process parameters such as fibre tension, mandrel rotational speed, liner internal pressure, ply drop off and turn around, and physical properties of resin (temperature and viscosity) can substantially affect the strength and quality of the filament wound pressure vessels. Additionally, the layup pattern of the hoop and helical plies also strongly affects the overall mechanical behaviour of the composite overwrapped pressure vessel (COPV). The microscopy of the tested composite pressure vessel is performed to study the distribution of the resin and fibres across the radial and meridional directions of the overwrapped composite laminate. Various imperfections like porosities, delamination, fibre cracking, accumulation of resin and dry fibres in localized regions are observed during microscopy. The experimentation cost for the prediction of the mechanical behaviour of composite overwrapped pressure vessel (COPV) under static and dynamic loading conditions is quite high which emphasizes the utilization of the finite element methods during the preliminary design stage. Finite element (FE) modelling of the composite overwrapped pressure vessel (COPV) requires a high-quality mesh model of overwrapped composite laminate along with the accurate assignment of material orientation to each element of the composite ply. A comparison of different modelling and analysis tools, such as ComposicaD and WoundSim, along with other methodologies, is conducted to develop a high-fidelity finite element (FE) model for the analysis of the composite overwrapped pressure vessels (COPV). Every tool has its own advantages and disadvantages, and it is observed that the best suitable methodology can be developed by combining positive features of multiple tools. Finally, the converged mesh model obtained from HyperMesh software is employed to study the static and dynamic behaviour of composite overwrapped pressure vessel (COPV).
File(s)
Document(s)
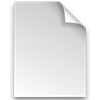

Description:
Size: 5.61 MB
Format: Adobe PDF
Cite this master thesis
APA
Ali, N. (2023). Simulation workflow of filament wound carbon composite tanks for pressurized hydrogen storage. (Unpublished master's thesis). Université de Liège, Liège, Belgique. Retrieved from https://matheo.uliege.be/handle/2268.2/18048
Chicago
The University of Liège does not guarantee the scientific quality of these students' works or the accuracy of all the information they contain.