Final work : Numerical investigation of the influence of geometric uncertainties on transonic compressor flows
Palmese, Claudio
Promoteur(s) :
Hillewaert, Koen
Date de soutenance : 4-sep-2023/5-sep-2023 • URL permanente : http://hdl.handle.net/2268.2/18223
Détails
Titre : | Final work : Numerical investigation of the influence of geometric uncertainties on transonic compressor flows |
Auteur : | Palmese, Claudio ![]() |
Date de soutenance : | 4-sep-2023/5-sep-2023 |
Promoteur(s) : | Hillewaert, Koen ![]() |
Membre(s) du jury : | Terrapon, Vincent ![]() Klausmann, Fabian |
Langue : | Anglais |
Nombre de pages : | 60 |
Mots-clés : | [en] Turbomachinery [en] CFD [en] Compressors [en] Transonic compressors [en] Axial compressors [en] Geometric uncertainty |
Discipline(s) : | Ingénierie, informatique & technologie > Ingénierie aérospatiale |
Public cible : | Chercheurs Professionnels du domaine |
Institution(s) : | Université de Liège, Liège, Belgique |
Diplôme : | Master en ingénieur civil en aérospatiale, à finalité spécialisée en "turbomachinery aeromechanics (THRUST)" |
Faculté : | Mémoires de la Faculté des Sciences appliquées |
Résumé
[en] Modern aeronautical engine development relies on a good computational prediction of flow quantities within the design process. Besides potential limitations in CFD related to flow modelling, a non-neglectable source of error can be related to geometric differences between the design and the final product, caused by wear and tear and manufacturing uncertainties. These variations do not simply impact the global performance of the machine, but may also give rise to flow phenomena that could change the stability limits of the machine or cause increased wear.
The Institute of Gas Turbines and Aerospace Propulsion at Technical University of Darmstadt conducted experiments in a 1.5-stage transonic axial compressor within the ARIAS project, funded by the Horizon2020 programme. In these measurements, a blade-to-blade variation in flow quantities could be observed at the rotor tip with Particle Image Velocimetry and unsteady pressure measurements.
The aim of this work is hence to analyse the influence on the compressor flow of potential geometric uncertainties in the rotor blades by means of a parametrization of the original CAD geometry. By doing so, it becomes possible to set up an automated script that generates blades which differ from the standard in one or more aspects, according to real geometric variations. A feasible reference domain of the 1.5 stage transonic compressor is first created with the CAD model and analysed. Then, the rotor blade is parametrized and compared both in geometry and performance to the reference setup. The parametrized blade is then used as a base to generate sets of modified blades, which are each studied in single-passage simulations in order to compare the consequent flow variations. Finally, a full-annulus simulation is set up where only a single blade is modified in its stagger angle, with the objective of capturing blade-to-blade flow variations.
The flow seems to be highly sensitive to leading edge curl, with significant sensitivity to trailing edge curl and leading edge thickness, while limited change was recorded with the chosen amount of stagger angle change. When misstaggering a single blade, passage-to-passage variations were found in blade loading, shock positioning, and others, with some rotor outlet quantities displaying weak patterns in the circumferential direction in the tip and hub regions.
Fichier(s)
Document(s)
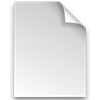

Description: The full report, corrected as indicated by adding the jury members
Taille: 14.78 MB
Format: Adobe PDF
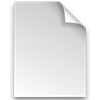

Description: Summary pages with figures, corrected with addition of jury members as indicated
Taille: 6.12 MB
Format: Adobe PDF
Citer ce mémoire
APA
Palmese, C. (2023). Final work : Numerical investigation of the influence of geometric uncertainties on transonic compressor flows. (Unpublished master's thesis). Université de Liège, Liège, Belgique. Retrieved from https://matheo.uliege.be/handle/2268.2/18223
Chicago
L'Université de Liège ne garantit pas la qualité scientifique de ces travaux d'étudiants ni l'exactitude de l'ensemble des informations qu'ils contiennent.