Fatigue Analysis of Floating Offshore Wind Turbine Tower in Composite Material
Al-Ghuwaidi, Abdulelah Abdullah Saleh
Promotor(s) :
Rigo, Philippe
Academic year : 2022-2023 • Permalink : http://hdl.handle.net/2268.2/19333
Details
Title : | Fatigue Analysis of Floating Offshore Wind Turbine Tower in Composite Material |
Author : | Al-Ghuwaidi, Abdulelah Abdullah Saleh ![]() |
Advisor(s) : | Rigo, Philippe ![]() |
Language : | English |
Discipline(s) : | Engineering, computing & technology > Mechanical engineering |
Funders : | Bureau Veritas Marine & Offshore |
Research unit : | Research Department, Composite Section |
Target public : | Researchers Professionals of domain Student General public Other |
Institution(s) : | Université de Liège, Liège, Belgique |
Degree: | Master : ingénieur civil mécanicien, à finalité spécialisée en "Advanced Ship Design" |
Faculty: | Master thesis of the Faculté des Sciences appliquées |
Abstract
[en] The expansion in the offshore wind industry is growing rapidly due the substantial amount
of energy it can generate. Floating Offshore Wind Turbines (FOWT) have high potential in
the energy market for sites with deep water depths. However, these FOWT’s platforms are
subjected to high dynamic coupling loads which can lead to fatigue in their substructures.
The superior properties of FRP materials including better corrosion-resistance, strengthto-
weight ratio and fatigue performance make them better candidates compared to steel.
As the size of structures increases, the advantages of steel diminish. However, the lack of
design guidelines and rules along with technological limitations highlight a research gap
for the use of FRP materials in the offshore renewable industry. Unlike other aspects of
FOWTs such as foundations, the tower linking the turbine and foundation has not been a
primary focus of innovation. The FibreGY project aims to enable the use FRP materials
in the marine renewable sector particularly in large offshore wind and tidal platforms. In
this thesis, the fatigue analysis of a semi-submersible twin-turbine FOWT tower made
with composite materials will be performed. Bureau Veritas (BV) software HydroStar will
be used for the FOWT hydrodynamic response. The newly in-house software OPERA
developed within the research department of BV Marine and Offshore will be used for the
FOWT global response under environmental loads. The stresses within the FRP tower
will be obtained by using the analytical model developed in this thesis in a Python script.
BV fatigue guidelines will be used to assess the fatigue life of the FRP tower. Design
optimization of the FRP tower will be carried out using the developed Python tools for
the fatigue life and BV ComposeIT software for the static analysis. FEMAP software will
be used for FOWT modelling, static analysis, buckling and modal analysis. The results
show that the fatigue damage of the FRP tower using carbon fibre and epoxy resin is
very low and sufficient for 20 years design life. The design optimization of the FRP tower
shows a reduction of nearly 66% in weight compared to the original total weight with
the reference laminates. The optimized FRP tower is able to withstand static loads and
fatigue damage while respecting the deflection and buckling criteria.
File(s)
Document(s)
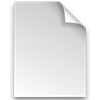

Description:
Size: 21.9 MB
Format: Adobe PDF
Cite this master thesis
APA
Al-Ghuwaidi, A. A. S. (2023). Fatigue Analysis of Floating Offshore Wind Turbine Tower in Composite Material. (Unpublished master's thesis). Université de Liège, Liège, Belgique. Retrieved from https://matheo.uliege.be/handle/2268.2/19333
Chicago
The University of Liège does not guarantee the scientific quality of these students' works or the accuracy of all the information they contain.