Master thesis and internship[BR]- Master Thesis : Improvement and validation of a robotized and autonomous experimental test bench to characterize blisks dynamics[BR]- Integration Internship : V2i
Bourguignon, Adrien
Promotor(s) :
Salles, Loïc
Date of defense : 26-Jan-2024 • Permalink : http://hdl.handle.net/2268.2/19547
Details
Title : | Master thesis and internship[BR]- Master Thesis : Improvement and validation of a robotized and autonomous experimental test bench to characterize blisks dynamics[BR]- Integration Internship : V2i |
Author : | Bourguignon, Adrien ![]() |
Date of defense : | 26-Jan-2024 |
Advisor(s) : | Salles, Loïc ![]() |
Committee's member(s) : | Kerschen, Gaëtan ![]() Dimitriadis, Grigorios ![]() |
Language : | English |
Number of pages : | 68 |
Discipline(s) : | Engineering, computing & technology > Aerospace & aeronautics engineering |
Institution(s) : | Université de Liège, Liège, Belgique |
Degree: | Master en ingénieur civil en aérospatiale, à finalité spécialisée en "aerospace engineering" |
Faculty: | Master thesis of the Faculté des Sciences appliquées |
Abstract
[en] Bladed disks play crucial roles in various engineering applications, particularly within turbine engine rotors. Typically, in analysis, each segment of a bladed disk is assumed to be identical, forming the basis for a single-sector model. Nevertheless, real-world bladed disks exhibit inevitable variations among individual segments due to factors like manufacturing tolerances, operational wear, and other influences. This phenomenon, referred to as mistuning, introduces discrepancies that can yield signifi- cant impacts. Even minor instances of mistuning can substantially alter the vibration characteristics of a bladed disk when compared to an ideally tuned system. Notably, this can lead to concentrated vibration energy in specific blades, resulting in increase stress levels and fatigue concerns.
Contemporary designs have introduced one-piece assemblies of bladed disks known as blade inte- grated disks, or blisks, which offer clear advantages in terms of performance, cost, and mass reduction. However, these designs pose challenges for mechanical engineering due to the exacerbated effects of mistuning. This is primarily attributed to the structure’s low damping, increased disk flexibility, and the coupling between blades and the disk.
Hence, a precise method for identifying mistuning is crucial for manufacturers to prevent potential engine failures. The methodology presented by the V2i company involves a comprehensive automated system for mistuning identification, aiming for minimal human intervention and improved accuracy. This approach employs the Inverse Component Mode Mistuning (ICMM) technique for mistuning iden- tification, with the mistuning pattern determined after completing experimental measurements. To achieve this, the blisk is fixed to an electrodynamic shaker, and vibration measurements are conducted using an infrared Laser Doppler Vibrometer mounted on a robotic arm. The use of a robotic mea- surement system offers advantages that are unreachable in manual methods, including the ability to perform 3D measurements, precise and reproducible positioning, and rapid measurement of numerous points without human involvement.
Initially, this thesis addresses the challenge of selecting a minimal set of measurement locations for mistuning experimental modal testing in a test industrial blisk. The selection process employs the Effective Independence Distribution Vector method in conjunction with a technique based on the maximum displacement amplitude of deformation. Subsequently, an alternative method for mistuning identification is explored for potential improvements. Leveraging experimental measurements, the study implements the Integral Mode Mistuning (IMM) method, an extension of the Component Mode Mistuning (CMM) approach, and conducts a comparative analysis against the ICMM method.
The investigation reveals that the optimal laser measurement locations are located at the blade tips on both the leading and trailing edges, thereby validating the proposed methodology. Mistuning is then computed using both the ICMM and IIMM methods. While the IIMM method accounts for blade-drum coupling, it involves higher computational costs. The results of the structure considered demonstrate that both methods exhibit similar trends, therefore implying that the blisk under con- sideration does not exhibit mistuning in the disk part. The conclusion is that the ICMM method is more fitted in this specific context due to its lower computational time.
File(s)
Document(s)
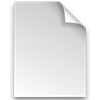

Description:
Size: 28.47 MB
Format: Adobe PDF
Cite this master thesis
APA
Bourguignon, A. (2024). Master thesis and internship[BR]- Master Thesis : Improvement and validation of a robotized and autonomous experimental test bench to characterize blisks dynamics[BR]- Integration Internship : V2i. (Unpublished master's thesis). Université de Liège, Liège, Belgique. Retrieved from https://matheo.uliege.be/handle/2268.2/19547
Chicago
The University of Liège does not guarantee the scientific quality of these students' works or the accuracy of all the information they contain.