Travail de fin d'études et stage[BR]- Travail de fin d'études : Towards the Integration of Casting Simulations to a Structural Topology Optimization Framework[BR]- Stage d'insertion professionnelle
Yi Mon Theint
Promotor(s) :
Tromme, Emmanuel
Date of defense : 26-Jan-2024 • Permalink : http://hdl.handle.net/2268.2/19569
Details
Title : | Travail de fin d'études et stage[BR]- Travail de fin d'études : Towards the Integration of Casting Simulations to a Structural Topology Optimization Framework[BR]- Stage d'insertion professionnelle |
Translated title : | [en] Towards the Integration of Casting Simulations to a Structural Topology Optimization Framework |
Author : | Yi Mon Theint ![]() |
Date of defense : | 26-Jan-2024 |
Advisor(s) : | Tromme, Emmanuel ![]() |
Committee's member(s) : | Béchet, Eric ![]() Duysinx, Pierre ![]() Fernandez Sanchez, Eduardo Felipe ![]() |
Language : | English |
Number of pages : | 60 |
Keywords : | [en] topology optimization, manufacturing, casting, constraints, flows with heat transfer, OpenFOAM |
Discipline(s) : | Engineering, computing & technology > Mechanical engineering |
Target public : | Researchers Professionals of domain Student |
Institution(s) : | Université de Liège, Liège, Belgique |
Degree: | Master en ingénieur civil mécanicien, à finalité spécialisée en technologies durables en automobile |
Faculty: | Master thesis of the Faculté des Sciences appliquées |
Abstract
[en] Cost-effective lightweight design emerges as a pivotal focus for the automotive industry's future. Global competitiveness, stringent regulatory standards, and the integration of weight-intensive electronic elements in modern propulsion systems require the development of lighter, more efficient chassis components.
With this perspective, topology optimization is extensively applied for the design of lightweight components. The casting process stands as a time and cost-efficient method for automotive mass production, widely adapted within the industry. Typically, weight optimization process does not consider castability, leading to later-stage modifications . These modifications incur additional time spent for manufacturability and often result in a heavier design than the initially optimized one. This thesis introduces an optimization process that optimizes weight and castability concurrently during the early design phase, offering a solution to this challenge.
The study focuses on incorporating casting simulations into previously developed topology optimization framework, which involves accommodating geometric casting constraints, including directional molding, split-drawing, minimum member size, and draft angle considerations. A previously established Python code, designed for topology optimization incorporating casting constraints, offers flexibility and scalability. This code utilizes the open-source FEniCS Project as its finite element software, enabling the utilization of PETSc as a backend for linear algebra operations to enhance efficiency. A casting simulation is performed using OpenFOAM, focusing on flows involving heat transfer. A dedicated solver, employing the continuous adjoint approach, is implemented within OpenFOAM to calculate sensitivities. These outcomes are then merged with the topology optimization optimizer in FEniCS, leading to the establishment of an integrated optimization approach.
The established solver undergoes validation by comparing the sensitivities computed with the finite difference method. Subsequently, the integrated approach's validation is carried out through a 2-dimensional cantilever beam problem.
File(s)
Document(s)
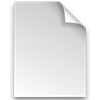

Description:
Size: 5.17 MB
Format: Adobe PDF
Annexe(s)
Cite this master thesis
The University of Liège does not guarantee the scientific quality of these students' works or the accuracy of all the information they contain.