Design Optimization and Evaluation of Variable Profile Propellers using Panel Method
Baqir Ali
Promotor(s) :
Rigo, Philippe
Academic year : 2023-2024 • Permalink : http://hdl.handle.net/2268.2/22242
Details
Title : | Design Optimization and Evaluation of Variable Profile Propellers using Panel Method |
Translated title : | [fr] Design Optimization and Evaluation of Variable Profile Propellers using Panel Method |
Author : | Baqir Ali ![]() |
Advisor(s) : | Rigo, Philippe ![]() |
Language : | English |
Discipline(s) : | Engineering, computing & technology > Mechanical engineering |
Funders : | Mecklenberger Metallguss GmbH |
Name of the research project : | Design Optimization and Evaluation of Variable Profile Propeller using Panel Method |
Institution(s) : | Université de Liège, Liège, Belgique University of Rostock, Rostock, Germany |
Degree: | Master : ingénieur civil mécanicien, à finalité spécialisée en "Advanced Ship Design" |
Faculty: | Master thesis of the Faculté des Sciences appliquées |
Abstract
[en] Evaluation and Optimization of open water performance of variable profile propellers is conducted in this thesis. Variable profiles are generated by changing the radial distribution of
camber of single NACA profile and by combining two different NACA profiles. CAESES is
used for propeller modelling, parametrization and optimization. It is coupled with the panel
code based solver panMARE for optimization of the design point evaluated using thrust
identity method. Optimized solutions are validated using RANSE based CFD solver and top
performing candidates are checked for cavitation using panMARE. It is observed that the
variation of camber at normalized radial location of 0.6 has a significant impact on power.
Performance improvement is observed for single profile blades but discrepancies between optimization results and CFD validation are observed, attributed to modelling defects and panel
code method’s limitations. Moreover, exploration of propeller blade with combination of two
profiles indicated that the minimum power configuration is achieved when profile switching
occurs at normalized radial location of 0.9, although actual performance improvement is not
observed due to limitations in the correction factors used.
File(s)
Document(s)
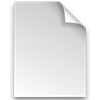

Description:
Size: 6.2 MB
Format: Adobe PDF
Cite this master thesis
APA
Baqir Ali (2024). Design Optimization and Evaluation of Variable Profile Propellers using Panel Method. (Unpublished master's thesis). Université de Liège, Liège, Belgique. Retrieved from https://matheo.uliege.be/handle/2268.2/22242
Chicago
The University of Liège does not guarantee the scientific quality of these students' works or the accuracy of all the information they contain.