Identification and analysis of vibration sources in a micro-CMG
Noiset, Guillaume
Promotor(s) :
Kerschen, Gaëtan
Date of defense : 25-Jun-2020/26-Jun-2020 • Permalink : http://hdl.handle.net/2268.2/9085
Details
Title : | Identification and analysis of vibration sources in a micro-CMG |
Translated title : | [fr] Identification et analyse des sources de vibrations au sein d'un micro-CMG |
Author : | Noiset, Guillaume ![]() |
Date of defense : | 25-Jun-2020/26-Jun-2020 |
Advisor(s) : | Kerschen, Gaëtan ![]() |
Committee's member(s) : | Bruls, Olivier ![]() Collette, Christophe ![]() Demonty, Julien |
Language : | English |
Number of pages : | 54 |
Keywords : | [en] Micro-CMG [en] Vibrations [en] Experimentation |
Discipline(s) : | Engineering, computing & technology > Aerospace & aeronautics engineering |
Institution(s) : | Université de Liège, Liège, Belgique |
Degree: | Master en ingénieur civil en aérospatiale, à finalité spécialisée en "aerospace engineering" |
Faculty: | Master thesis of the Faculté des Sciences appliquées |
Abstract
[en] Control moment gyroscopes are efficient systems of attitude control for satellites. As every rotating assembly, they produce undesirable vibrations in spacecrafts. Instead of isolating the satellite from these systems to prevent the spread of the perturbations, it is important to first decrease the generation of vibrations itself. The main vibration sources have been identified as the balance of the flywheel, the impurities in the bearings and the motor ripple.
The key parameters influencing the generation of the vibrations explored in this work are the balance of the wheel, the preload, the contact angle and the quality of the bearings. An experimental set-up is then designed to highlight their impact on the frequency spectrum: an aluminium structure embracing a bearing pair holds the flywheel concentric with the axis of the motor. To study all the key parameters, the set-ups use several pairs of bearings and wheels. By adapting the rotation speeds, the flywheel, the bearings and the preload, multiple test plans are elaborated to compare the influence of the various parameters.
Preliminary studies prove that the structure is fit to sustain the applied loads. Further, they predict an optima speed of 4,000 RPM for an ideal lubricant layer in the bearings, reducing the friction while providing good wear protection. A last study predicts a maximum rotation speed of about 5,000 RPM, due to the grease generating high friction, while the driving torque is limited.
The different protocols established in this work aim at highlighting a decrease of the vibration generation through a lower preload, a balanced wheel and high quality bearings protected from external bodies.
File(s)
Document(s)
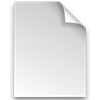

Description: -
Size: 16.29 MB
Format: Adobe PDF
Annexe(s)
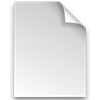

Description: Résumé du travail
Size: 58.45 kB
Format: Adobe PDF
Cite this master thesis
APA
Noiset, G. (2020). Identification and analysis of vibration sources in a micro-CMG. (Unpublished master's thesis). Université de Liège, Liège, Belgique. Retrieved from https://matheo.uliege.be/handle/2268.2/9085
Chicago
The University of Liège does not guarantee the scientific quality of these students' works or the accuracy of all the information they contain.