Closed-loop active shape control actuator
Gillet, Simon
Promotor(s) :
Collette, Christophe
Date of defense : 6-Sep-2021/7-Sep-2021 • Permalink : http://hdl.handle.net/2268.2/12882
Details
Title : | Closed-loop active shape control actuator |
Translated title : | [fr] Actionneur de forme à contrôle actif en boucle fermée |
Author : | Gillet, Simon ![]() |
Date of defense : | 6-Sep-2021/7-Sep-2021 |
Advisor(s) : | Collette, Christophe ![]() |
Committee's member(s) : | Loix, Nicolas
Béchet, Eric ![]() Bruls, Olivier ![]() |
Language : | English |
Number of pages : | 121 |
Keywords : | [en] Actuator [en] Sensor [en] Bearings |
Discipline(s) : | Engineering, computing & technology > Civil engineering Engineering, computing & technology > Aerospace & aeronautics engineering |
Institution(s) : | Université de Liège, Liège, Belgique |
Degree: | Master en ingénieur civil en aérospatiale, à finalité spécialisée en "aerospace engineering" |
Faculty: | Master thesis of the Faculté des Sciences appliquées |
Abstract
[fr] Today, ecology and CO2 emissions are at the centre of many debates. Because the aviation sector is a large emitter of CO2, the main manufacturers of the industry are trying to reduce the fuel consumption of the aircraft and thus the CO2 emissions. One of the technologies studied is the Hybrid Laminar Flow Control system, a combination of Natural Laminar Flow and Laminar Flow Control. Sonaca, being one of these manufacturers, is developing a Natural Laminar Flow profile leading edge. To do so, Sonaca in collaboration with Micromega Dynamics has to correct the wrong shape of a leading edge using an active control mechanism during its manufacturing process.
A description and comparison of actuators, sensors, guiding mechanisms and architecture controls that can be used in an active shape control mechanism are performed. Based on this analysis, two active shape control mechanisms are studied. The first mechanism is composed of three actuators that activate (push or pull) a rigid body attached to the skin of the leading edge. The second mechanism acts directly on the skin by pushing or pulling perpendicularly to the desired skin shape.
Since the correction using the first mechanism requires large forces, two methodologies of optimization are developed. After some investigation, this mechanism did not allow to correct properly the local errors appearing on the skin. This mechanism is therefore abandoned. The characteristics required for the second mechanism favour the choice of an electromechanical actuator connected to a jackscrew and controlled with a LVDT sensor.
File(s)
Document(s)
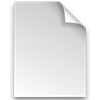

Description: -
Size: 24.6 MB
Format: Adobe PDF
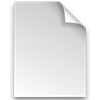

Description: -
Size: 96.07 kB
Format: Adobe PDF
Annexe(s)
Cite this master thesis
APA
Gillet, S. (2021). Closed-loop active shape control actuator. (Unpublished master's thesis). Université de Liège, Liège, Belgique. Retrieved from https://matheo.uliege.be/handle/2268.2/12882
Chicago
The University of Liège does not guarantee the scientific quality of these students' works or the accuracy of all the information they contain.